As far as pure energy goes, it doesn’t get better than solar energy. Photovoltaic (PV) energy technologies are improving and growing at an impressive rate. This industry hopes to be a major source of electrical energy on Earth in the not-too-distant future. At the rate it is growing, that will probably happen within 10 to 20 years. That sounds great but there is a dark side to the PV industry’s growth and it is in the way materials are facilitated to the complete installation of a PV system.
Before I talk about this environmental dark side of the solar PV industry it is worth noting its bright clean side. If all the energy required to manufacture and facilitate the installation of the PV system was derived from fossil fuels, it would take only two years of operation to offset that non-renewable fossil-fuel energy. As renewable energies become more dominant that figure will become shorter. Ultimately the process of offsetting the non-renewable, fossil-fuel energy required to manufacture and implement a PV system could be close to zero. Unfortunately, there is still an environmental dark side that has not been offset. This has to do with the negative effects of the front end and back end of product manufacturing, mining and packaging.
On the front end, mining is necessary to get the raw materials to manufacture PV cells, PV modules, inverters, batteries, support structures and electrical conductors. It is possible to reduce the effects of mining by using materials that are more plentiful in the Earth’s crust but there will always be a requirement for mining. It is also possible to recycle materials that are currently reaching the end of their useful life. The obstacle here is usually financial since it is often lower cost to mine for new raw materials than to recycle them from previously manufactured products containing these same raw materials. Interestingly, even if it takes less energy to recycle a material, it may be more difficult and more expensive to completely facilitate the recycling process. When recycling is disadvantaged by these economics, tax incentives or subsidies should be put in place to make recycling more lucrative. The back end of manufacturing is packaging.
Almost every manufactured product is packaged before being sent into the marketplace.
PV modules are packaged on wooded pallets with plastic separators. They are often wrapped in stretch plastic or they are packaged in pairs with cardboard. Plastic is a forever-material that is almost completely non-recyclable. Wood and cardboard-based packaging is much more recyclable. Its recycling should be encouraged though tax incentives or subsidies.
- Inverters are packaged in cardboard and protected internally with either Styrofoam, polystyrene or corrugated fiberboard. Styrofoam and polystyrene are forever-materials that are non-recyclable and should not be used. Paper based products like cardboard should be used instead.
- Batteries are typically packaged the same way as inverters but primarily with cardboard.
- Small balance-of-system components (BOS) are shipped in cardboard, plastic and they use bubble wrap and foam peanuts to secure the items during shipment.
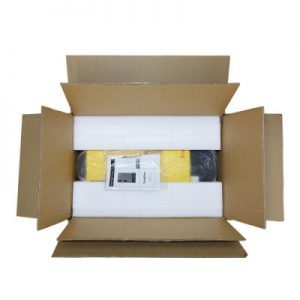
Packaging PV products with forever-products that are non-renewable and non-biodegradable is completely unacceptable. The purchaser of these products has a lot of influence over how these products a packaged; the best action is an email or phone call to the sales associate for the manufacturer as well as to the distributor of the products. Solar PV is a renewable product industry, we need to remove non-renewable, non-biodegradable products from the packaging process.
Kelly Provence
Solairgen, Inc.
IREC and NABCEP Certified PV Trainer
www.solairgen.com
706-867-0678
800-262-7560